AIM’S MANUFACTURING CAPABILITIES – A CUT ABOVE THE REST!
BACKGROUND
In preparation for exhibiting at Ecobuild, the Royal Institute of British Architects (RIBA) invited architects to pitch for the design of its ‘Bookshop and Meeting Space’, a landmark stand which would incorporate Rockpanel® into its structure, enable the presentation of its wide range of literature and host informal meetings at the show. Based on its innovative use of everyday materials on past projects, architects Freehaus were commissioned for the stand design and subsequently approached AIM to assist with the manufacture of the stand components – which enabled the company to utilise the full breadth of its bespoke CNC cutting capabilities and culminated in a high-profile presence for RIBA and Rockpanel at the show.
CHALLENGE
While Freehaus’ Ecobuild design was stand-out in terms of aesthetics, the practicalities of constructing the ‘RIBA Bookshop and Meeting Space’ proved slightly more challenging.
After the design was approved by RIBA, Freehaus was put under pressure to find a practical, professional and cost-effective solution to the stand build challenge within a very limited timeframe.
SOLUTION
The natural first step to identify a solution was to consult Rockpanel, who immediately referred Freehaus to AIM – a specialist manufacturer and preferred Rockpanel converter.
Gerald Roper, Rockpanel, comments: “We’ve worked with AIM for many years and they have consistently proven their ability to bespoke manufacture our product into virtually any form. The investment they have made in the production facilities, particularly the CNC cutting machine and the CAD design team, puts them in a unique position to be able to handle even the most challenging of demands.”
Based on AIM’s credentials in handling Rockpanel and its state-of-the-art manufacturing equipment, AIM was commissioned to manage the complete production of the stand components.
Starting with 24 Rockpanels at three metre lengths, AIM worked from CAD drawings to manufacture the materials into the required specification – which included the main stand structure as well as the furniture items.
Using its advanced CNC cutting machine, AIM used a combination of through-routing and surface-routing techniques to achieve a precise and high quality finish, with 1.5mm deep routing utilised to create striking and colourful graphics. This included the manufacture of 3050 x 1200mm Rockpanel Chameleon panels which were eventually constructed as a nine-metre long book display wall.
RESULTS
While the high-quality finish of the RIBA stand attracted much attention from visitors and fellow exhibitors, the real success of the project was turning a design vision into a practical reality – in a very short space of time.
From the perspective of Rockpanel, the precision manufacture of the stand components and AIM’s ability to interpret the CAD drawings and produce an accurate CNC mapping programme are what set the company apart as a leader in the converter market: “It’s one thing having the machine capabilities, it’s quite another having an experienced and expert technical team who can take CAD drawings and produce such an excellent match in real life. The attention to detail and the quality of the cutting which was achieved on the Ecobuild stand has made us consider future applications of Rockpanel that may have been previously discounted, “continues Gerald Roper.
Tim Dalton, General Manager, AIM, part of SIG Performance Technology, added: “This was the first time we’ve ever manufactured materials for a complete stand build out of Rockpanel… but that’s the nature of bespoke manufacture… everything is a first! Our CNC machines can be used to cut a broad range of construction materials with absolute precision and accuracy – the stand at Ecobuild is testament to that, it was an excellent project to deliver.”
“The technical team at AIM were extremely knowledgeable about Rockpanel as a material and worked closely with our own designers to produce a very high standard of workmanship. Their speed of response and attention to detail proved invaluable in the successful delivery of the project,” concluded Nick Gibbs, Project Architect.
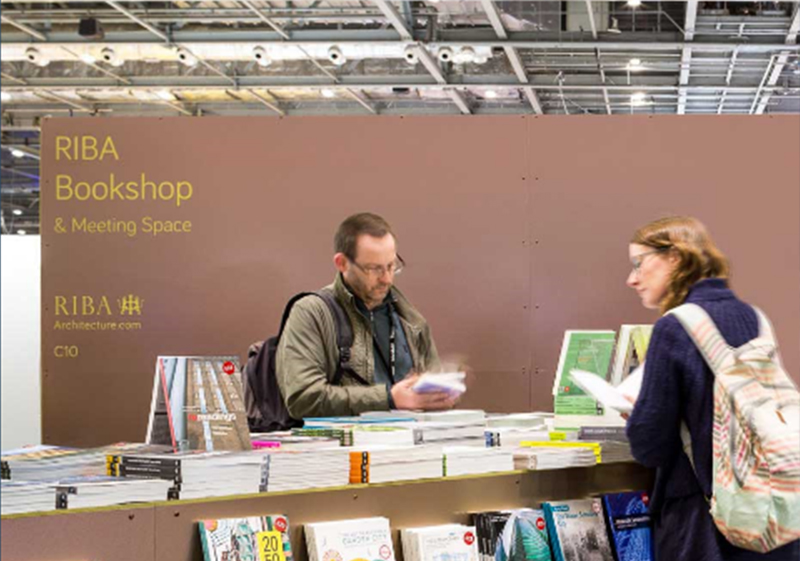